With Jessica up in Napa, and Nico recovering from being sick, I was on Daddy duty, and wouldn’t be able to get to the hangar. So instead, I brought the hangar home! Since the task I needed to complete was deburring of the ribs, and all the wheel work was complete, it was relatively easy to load up the ribs and scotch-brite pads and head home for an evening of deburring.
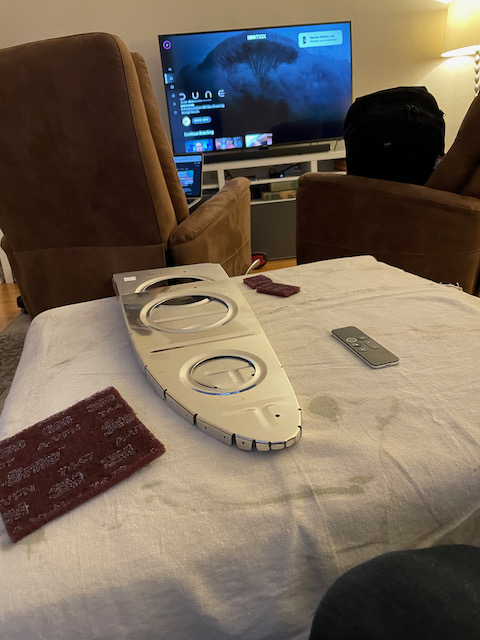
My task was to clean out all the small notches between the breaks in the rib flanges. I cut small pieces of scotch-brite, and scrubbed away until the edges felt smooth. One area I will go over with the wheel again is the leading edge flanges. I couldn’t get the smoothness of the “bumps” to my level of satisfaction. I have nightmares about micro bulges on the leading edge from not smoothing this out enough, but besides that, it was just a grind of an activity (no pun intended) that took over 5 hours spanning yesterday and today.
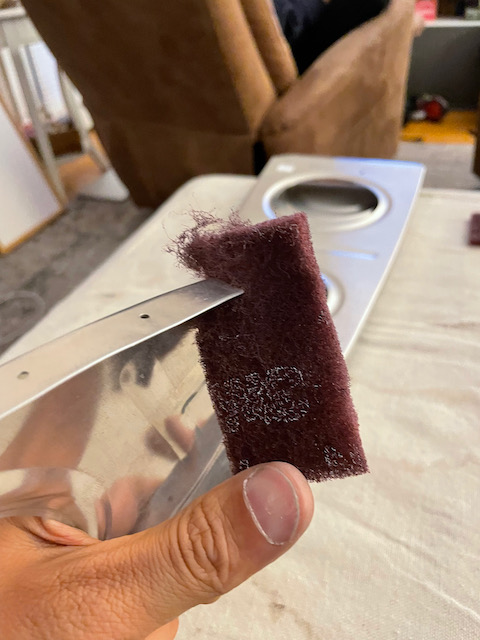

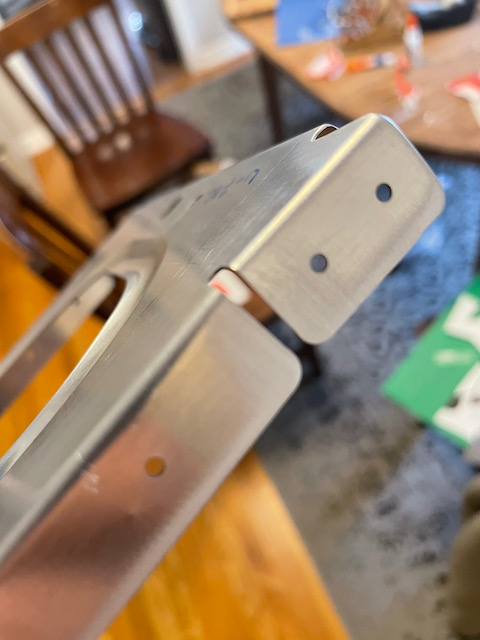
I found that by liberally trashing scotch-brite pads as soon as they wore down they remained effective. If I waited too long, it took too much time to get a good debur. If I were to do it again, I would have spent more time on the wheel, trying to get every possible nook and cranny possible. It is night and day how quickly work is done on the wheel verses a pad. live and learn.
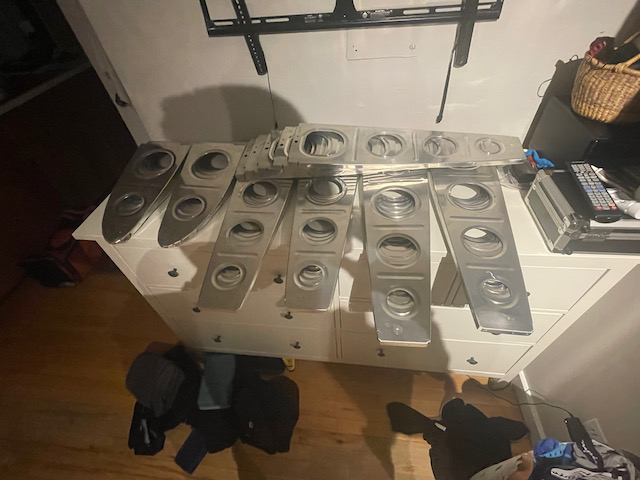
With all the ribs fully deburred, I will move on to the next step in preparing the ribs: bending rib flanges to 90˚. First I Need to build the special tool to make that job as easy as possible (see example below). I’ll get started on that today.
